The Cost of Neglecting Your Energy Systems
Written by Joe Wright
System maintenance is a critical part of a good energy management strategy that is often overlooked by many. Making sure that your energy intensive equipment is properly maintained isn’t just a good practice it’s a financial necessity and a must for sustainability. A lack of planning in this area is costing more than you might realise.
Why Maintenance Matters
Proper maintenance isn’t just about fixing things when they break. Ideally, you want to prevent problems before they arise and have a clear plan for upgrades and replacements at the right time. Every energy related system whether it’s heating, ventilation, and cooling (HVAC), manufacturing equipment, or electrical infrastructure requires some form of maintenance. Ignoring this essential task can lead to inefficiencies that increase costs and derail your energy saving goals.
The Hidden Cost of Neglect
When maintenance is ignored, systems become less efficient over time. Take an HVAC system, for example. A clogged air filter forces the system to work harder, consuming more energy. Now, scale that inefficiency across an entire facility running 24/7, and the costs skyrocket.
But inefficiency isn’t just about sustainability it’s about real money leaving your business unnecessarily. Running inefficient systems means higher energy bills, and waiting until something breaks to address an issue often leads to costly emergency repairs and operational downtime. In a manufacturing setting, unplanned downtime can directly impact production and revenue, causing further financial strain.
The Benefits of Proactive Maintenance
Companies that invest in proactive maintenance enjoy several key benefits:
- Lower Energy Bills – Well-maintained systems operate more efficiently, reducing overall energy consumption.
- Extended Equipment Lifespan – Regular upkeep prevents premature failure, delaying expensive replacements.
- Minimal Unplanned Downtime – Avoiding unexpected breakdowns keeps operations running smoothly and prevents lost revenue.
Implementing an Effective Maintenance Strategy
To ensure your energy systems are performing optimally, start with a structured maintenance plan tailored to your organisation’s needs. Your plan should include:
- Regular energy audits to identify inefficiencies and improvement opportunities.
- Routine inspections of key systems like HVAC, lighting, and production equipment.
- Staff training to help employees recognise early warning signs of inefficiency.
A good starting point is checking manufacturer recommendations for your equipment’s maintenance requirements. You might also consider aligning with recognised standards such as SFG20, which provides industry best practices for maintenance schedules.
Take Action Now
The best maintenance approach is one that fits your specific operational needs. If you already have a maintenance plan, assess whether it’s delivering results. If not, it’s time to make improvements.
Not sure how well your organisation is managing energy system maintenance? Find out with our free Energy Management Scorecard.Taking action today could save you significant costs and bring you closer to your energy efficiency, compliance, and net zero goals.
Are you looking to improve your organisations energy management practices?
Take our Energy Management Scorecard quiz to assess your current strategies and identify areas for improvement. Click below for the free assessment
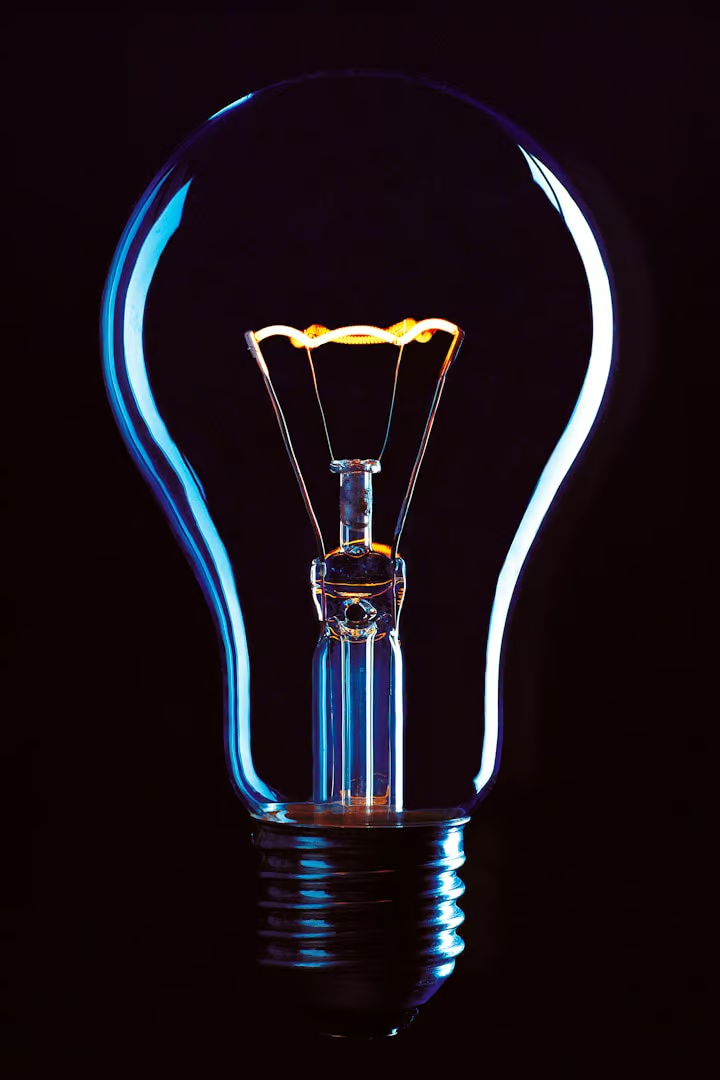
You May Also Like…
Compliance Simplified
If you’re part of any of the mandatory compliance scheme like SECR, ESOS, or the many others out there, then you...
Why maintenance matters for energy management
When you think about improving your energy management, where does your mind go first? Upgrades? New systems? Cutting...
Creating A Culture Of Energy Efficiency
If your business is subject to compliance schemes like ESOS or SECR, you’re not alone. A lot of the companies I work...